
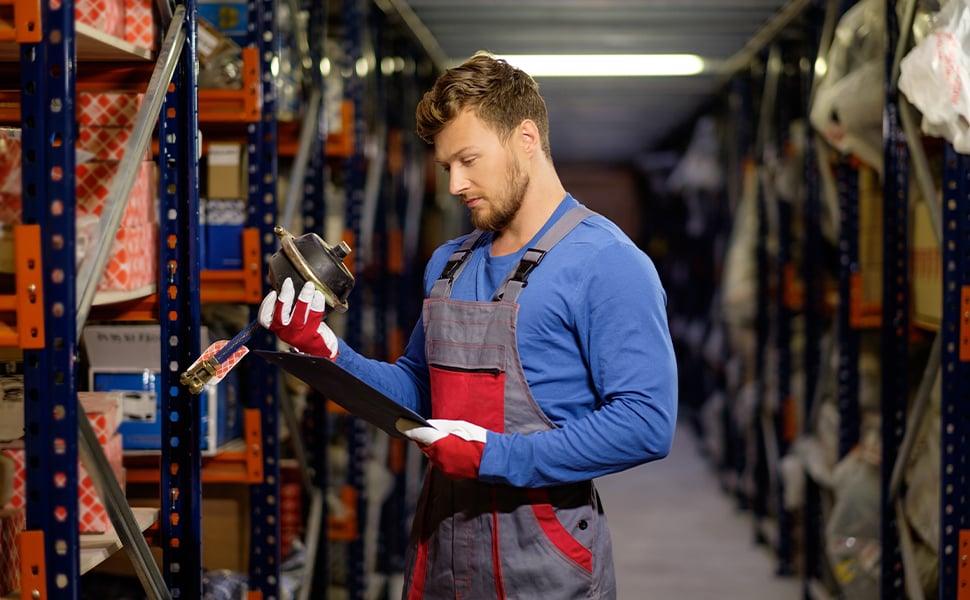
Although gut instinct, overstocking on everything “just in case,” and rush deliveries do sort of work, they cost the department a lot of money and your team a lot of frustration. Stop relying on “bad practices”įirst, you should commit to setting up a reliable system. Specifically, the current best practices and how we can start employing them. Now that we’ve covered the what and why of inventory control, let’s look at the how. What are some MRO inventory management best practices? For all the money organizations have tied up in inventory, on average, they’re only using at most 10% of it. In fact, according to Plant Services, between 90% and 92% of inventory goes unused annually. The second benefit is having the right parts and materials only when you need them, which can be a challenging balancing act. Instead of the production line sitting idle while everyone waits for a part to come in, techs can start right away, getting the line back up quickly.īut it’s more than just having the right parts and materials when you need them. And, when the press stops working because there’s a leak in the hydraulics, you have the right gasket or seal on hand to fix it. So, when that press hits X number of cycles, you have the right lubricant on hand for your preventive maintenance tasks.
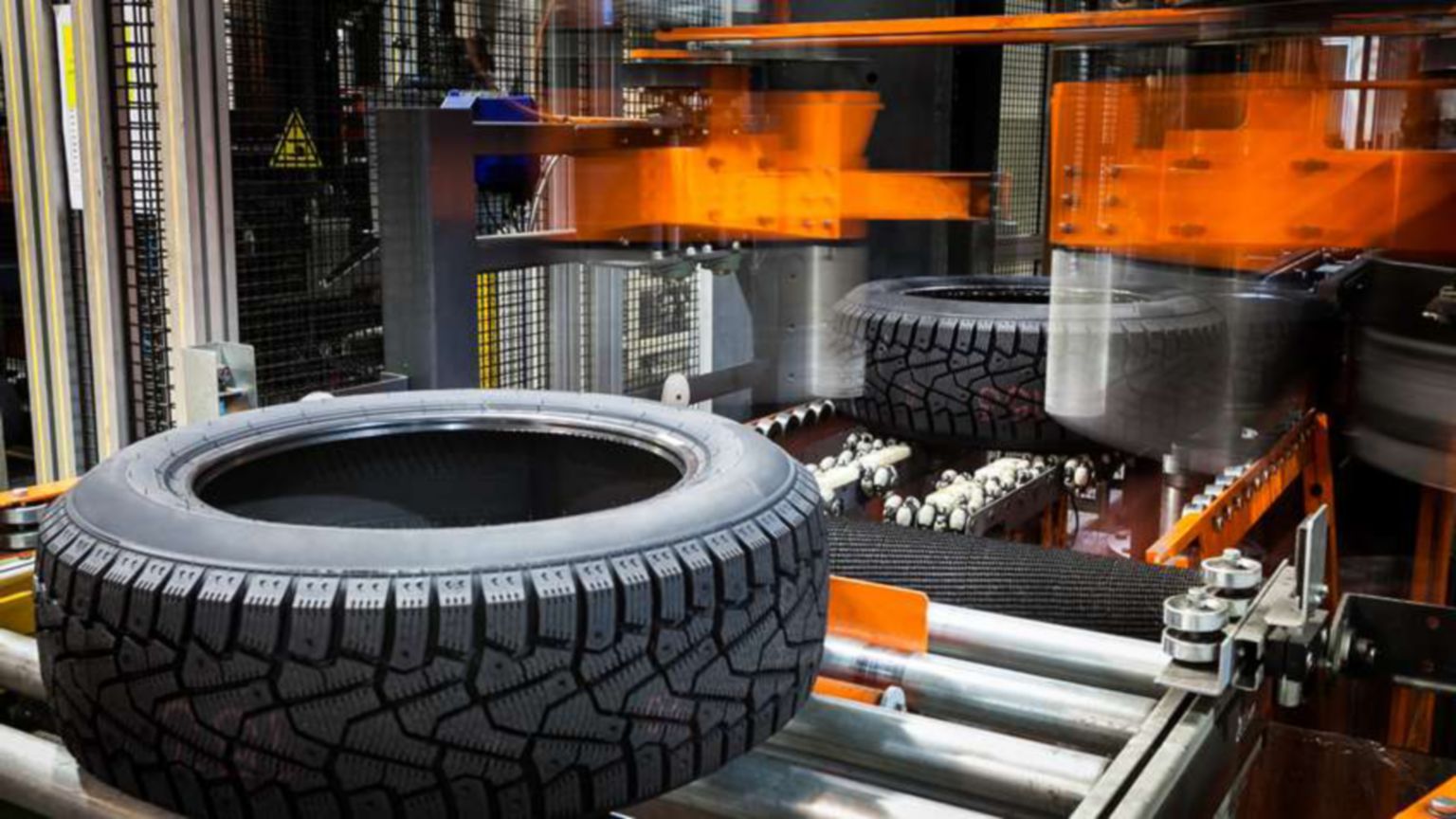
The first benefit of inventory management is having what you need to keep everything up and running. What are the benefits of MRO inventory management? The maintenance department is not the only one using MRO inventory, but MRO can represent a significant percentage of its budget.
#Mro inventory meaning software#
How do you get started? How do you use inventory management KPIs to track progress? And what role can modern inventory management software play in the whole process? How else can you ensure the maintenance team has the parts and materials they need right when they need them and at prices that don’t break your budget?īut there are plenty of other questions. There’s no question that you need efficient MRO inventory control.
